SUSTAINABLE HELIUM RECYCLING
A Helium Recovery System in leak testing is a sophisticated setup designed to capture and recycle helium gas used during the leak testing process. In industries where leak integrity is critical, such as aerospace, automotive, and refrigeration, helium is often the preferred test gas. This preference is due to helium’s small atomic size and inert nature, which allows it to quickly escape from even the smallest of leaks.
Components of an Helium Recovery System
The tracer gas recovery system consists of a series of components including compressors, filters, purifiers, and storage units. These components work together to collect the helium after it has passed through the test object, purify it from any contaminants, and compress it for reuse. This closed-loop process significantly enhances the efficiency of leak testing operations by minimizing helium wastage.
Benefits of Using a Recovery System
By implementing a helium recovery system, companies can achieve substantial cost savings, improve environmental sustainability, and ensure the reliability of their leak testing procedures. The efficient recycling of helium also reduces dependency on the supply chain for this valuable gas, making operations more resilient and cost-effective.
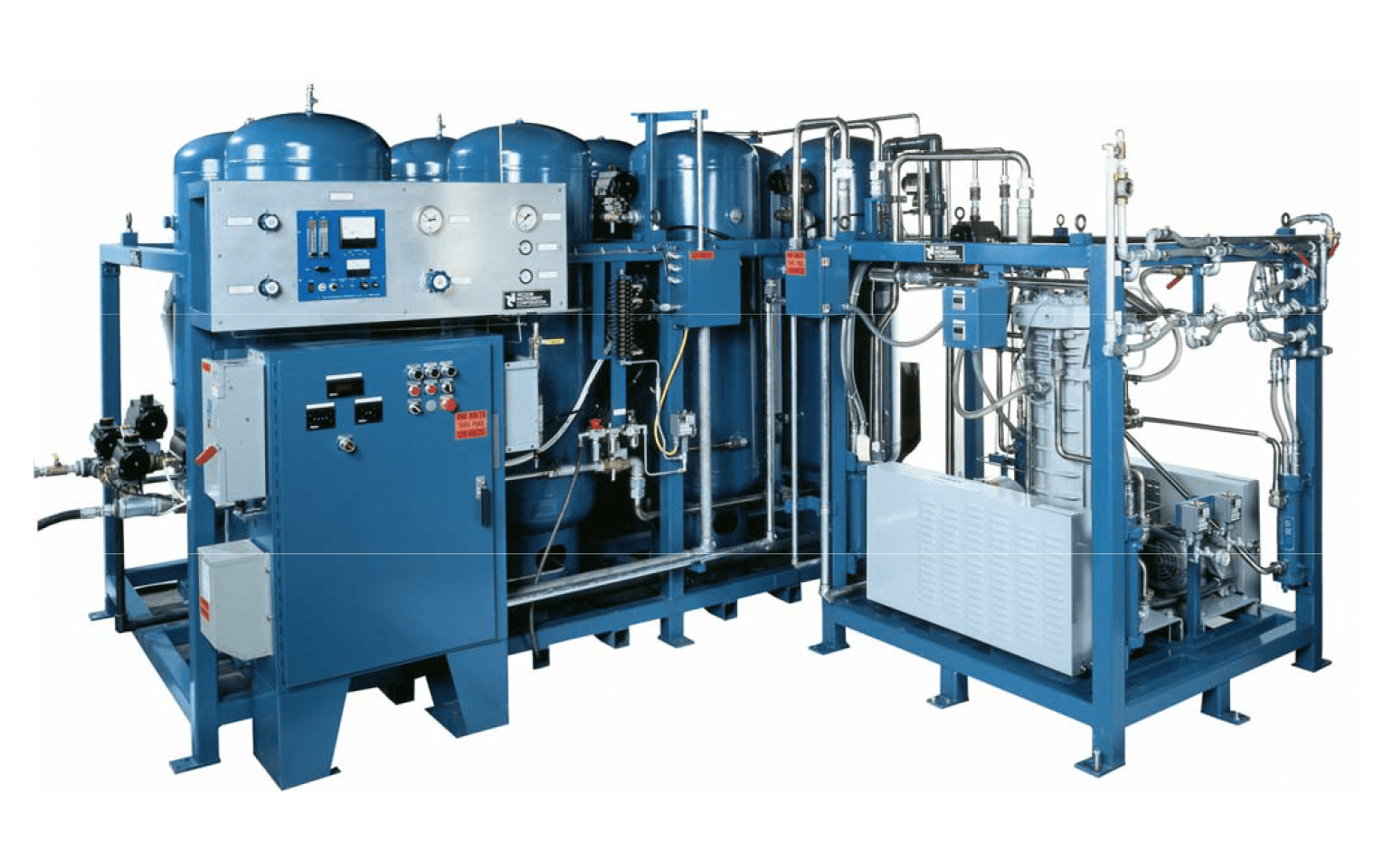
OUR SOLUTION
Introducing a solution to lower the cost associated with tracer gas consumption. While industries strive to meet increasing demands to offer higher quality products at lower prices, the need to efficiently recycle process gas becomes apparent.
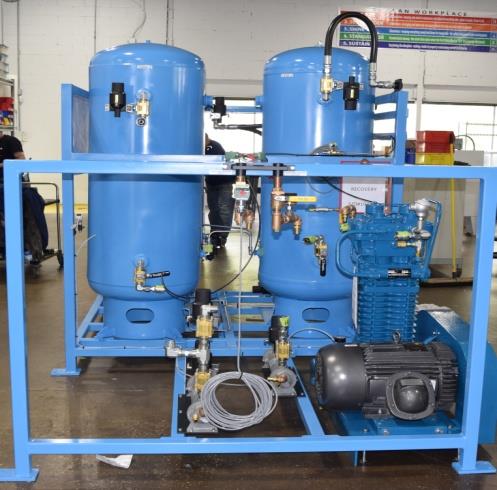
How it works
- The Gas Recovery Systems offered consists of ASME coded pressure tanks, a set of compressor(s), gas analyzer, microprocessor controls and all necessary valving, gas regulation and piping. The gas recovery operation includes these major steps:
- The tracer gas in the product is vented into the vacuum surge tank.
- During each stage of compression the tracer gas is passed through a set of high efficiency water cooled heat exchangers to remove the heat generated during compression.
- The final compressor outputs to tank completing the recycling operation.
Standard Sizes
- 4 SCFM
- 15 SCFM
- 25 SCFM
PRODUCT SPECIFICATIONS
Actual efficiency of 98% will be dependent on the product evacuation level prior to helium charge, final charge pressure, part pressure level at the completion of recovery, cycle time & product volume
Features
- Standalone programmable control packages
- Compressors utilizing an oil-less piston seal design to prevent oil contamination of the test object
- ASME coded and certified gas storage vessels
- Continuous tracer gas concentration monitoring and feedback ensures tracer gas percentage levels
- Real time diagnostics
- Automatic start-up operation
- Non-Lubricated cylinder and piston offer for ease of maintenance
- Cushioned valves designed for long life and quiet operation
- Piston rod seals of glass-filled self-lubricating Teflon, spring-loaded to compensate for lateral rod movement, wear and temperature variations
- HMI consists of a PanelView 800 screen
- Crankcases totally enclosed with an automatic breather valve to prevent entrance of dust or foreign matter
- Made in the USA
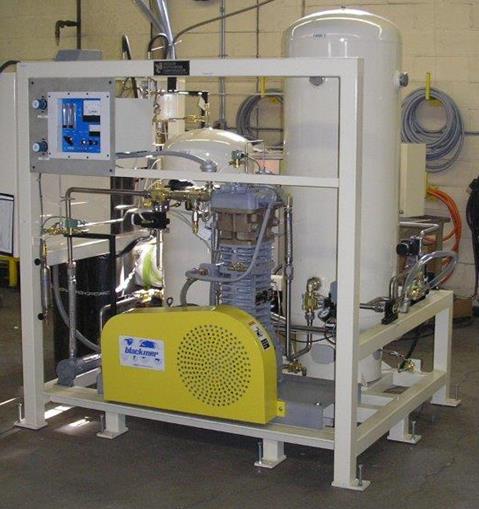
APPLICATIONS FOR VARIOUS INDUSTRIES
An innovative solution to lowering the cost associated with tracer gas consumption As industries strive to meet increasing demands to offer higher quality products at lower prices, the need to efficiently recycle process gas becomes apparent.
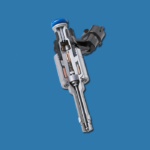
Fuel Injector
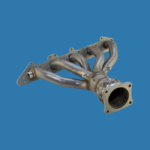
Exhaust Manifold
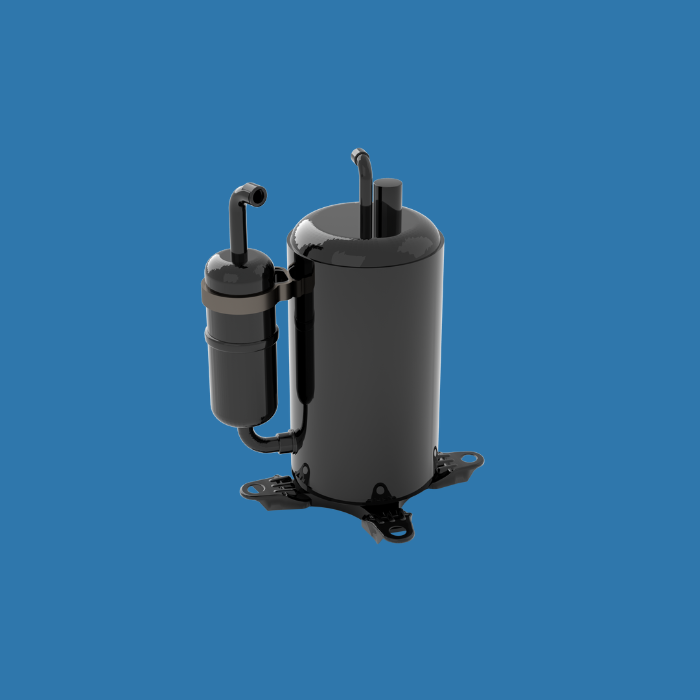
Compressors
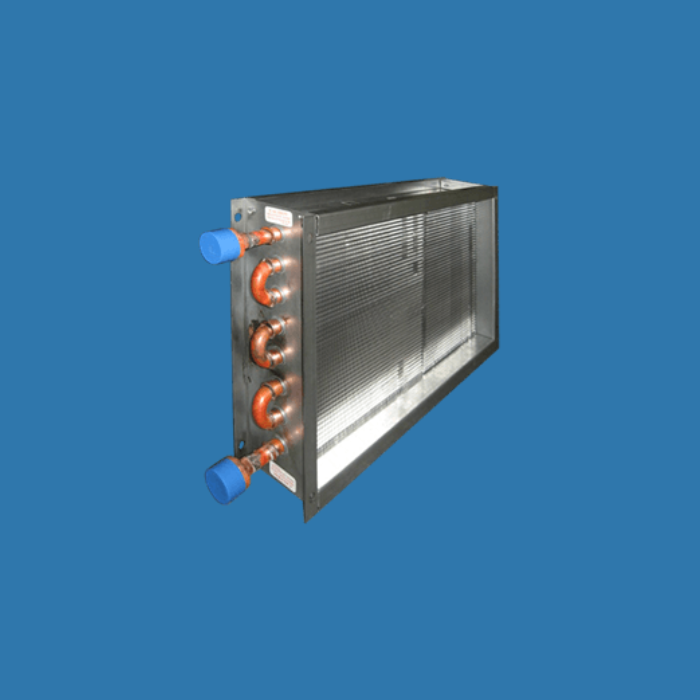
Coils
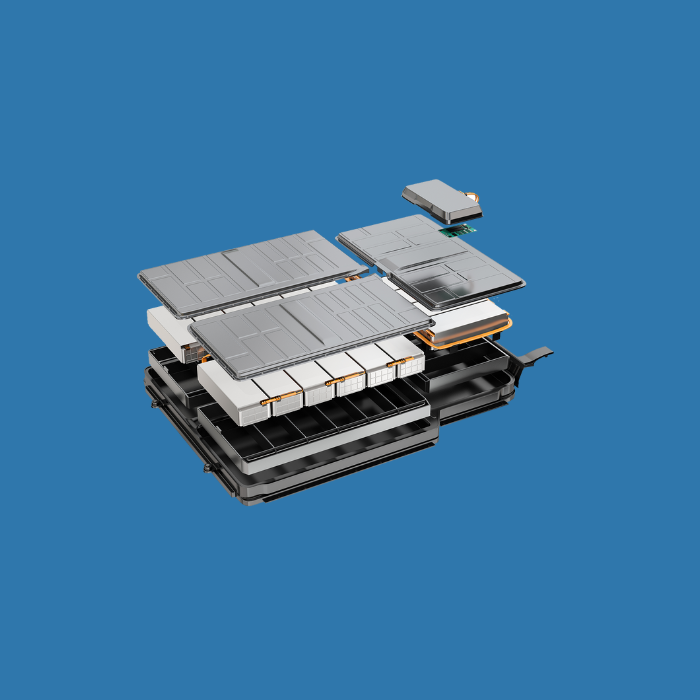
EV Battery
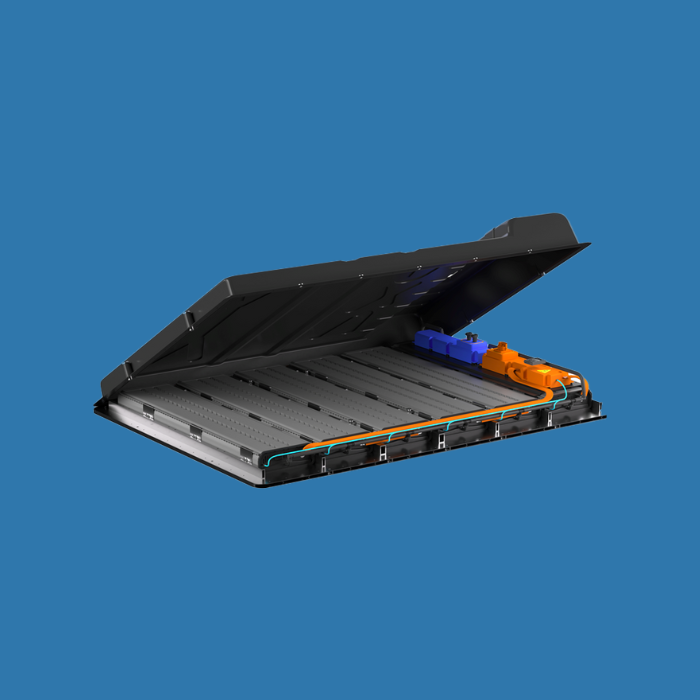
Housing
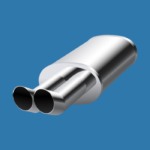
Exhaust Systems
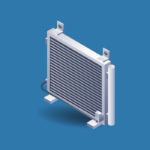
Cooling Circuits
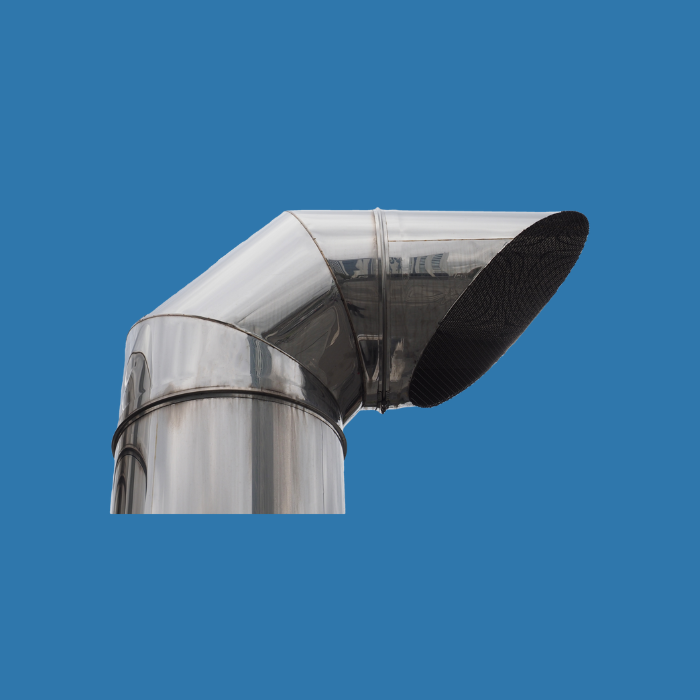
Tubings
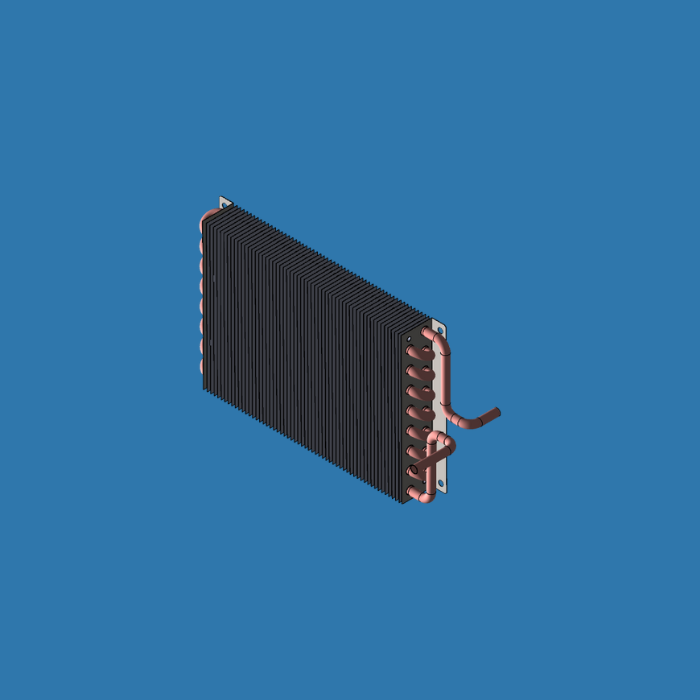
Heat Exchangers
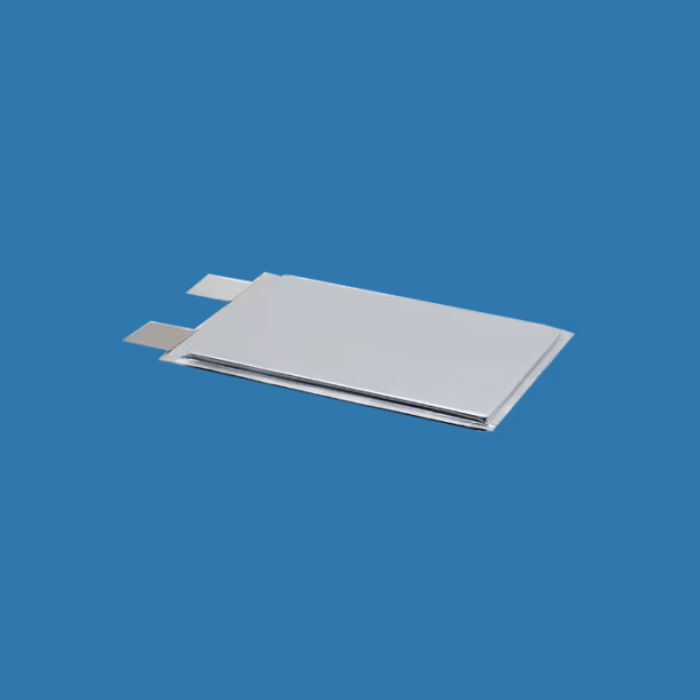
Pouches and Cells
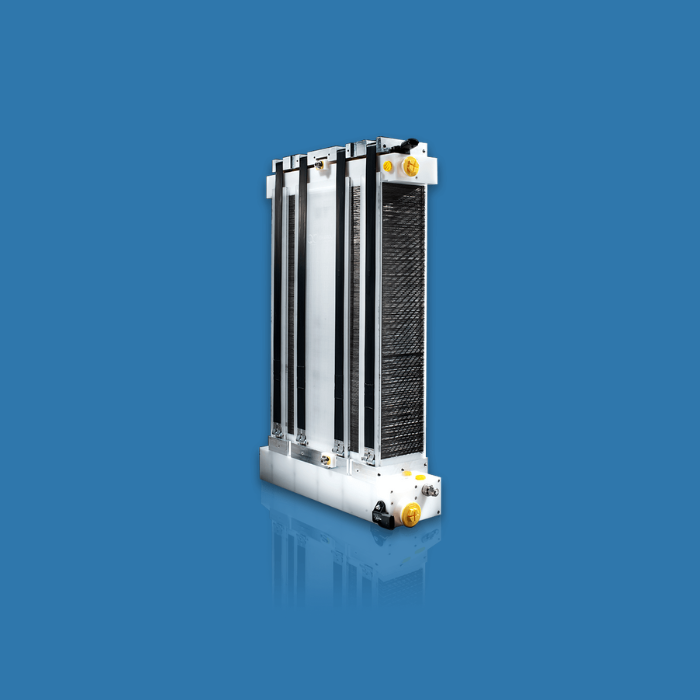
Fuel Cell Stack
Please contact us to request this document
Please contact us to request this document
Please contact us to request this document
Please contact us to request this document